Home / All / Power Coating Machine/Powder Spraying System /
Manual Powder Coating Paint Machine, Industrial Powder Coating Machines for Metal-PaintGo 660
Categories
- Industrial Pulse Jet Dust Collector
- Cyclone Dust Collector
- Wet Scrubber
- Solder/Welding Fume Extractor
- Pharmaceutical Dust Collector
- Sandblasting Dust Collector
- Metalworking Dust Collection System
- Laser Fume Extractor
- PE Sinter-plated Filter and Equipment
- Dust Collection Auxiliary Equipment
- Central Vacuum Cleaning System/Unit
- Industrial Centrifugal Fan
- Sand Blasting Machine
- Bag In Bag Out Filter System
- Power Coating Machine/Powder Spraying System
Manual Powder Coating Paint Machine, Industrial Powder Coating Machines for Metal-PaintGo 660
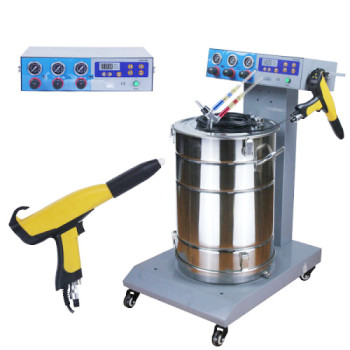


Categories | Power Coating Machine/Powder Spraying System |
---|---|
Brand | ACMAN |
Model | PaintGo-660 |
Update Time | Apr 3,2025 |
Detail Information
Paintgo-660, Add Pulse Mode and ,4 pre-programmed options for processing-Save 20% Powder Material!!!
Manual Powder Coating Paint Machine, Industrial Powder Coating Machines for Metal-PaintGo 660
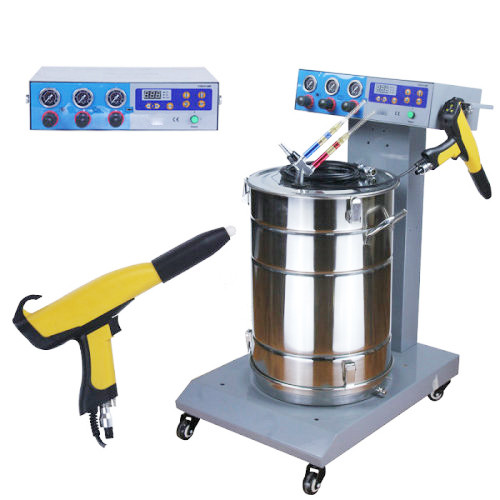
Portable Powder Coating Equipment Advantages
1: 100KV High Voltage:
Benefits: Faster Coating Speed, High Productivity
Benefits: Faster Coating Speed, High Productivity
2: High Voltage electrode in the powder gun:
Benefits: Making more powder with ions, save powder materials.
3: Advanced Controller:
Benefits: Precise Powder Output, Increasing utilization rate of raw power.
4: Multi-choices Nozzle: Super Cascade
Benefits: Ensuring perfect powder atomization, Improving surface quality.
5: Cleaning Mode:
Benefits: Fast color change, Non-stick material
Benefits: Making more powder with ions, save powder materials.
3: Advanced Controller:
Benefits: Precise Powder Output, Increasing utilization rate of raw power.
4: Multi-choices Nozzle: Super Cascade
Benefits: Ensuring perfect powder atomization, Improving surface quality.
5: Cleaning Mode:
Benefits: Fast color change, Non-stick material
Paintgo-660/What Powder Coating Machine Consist of?
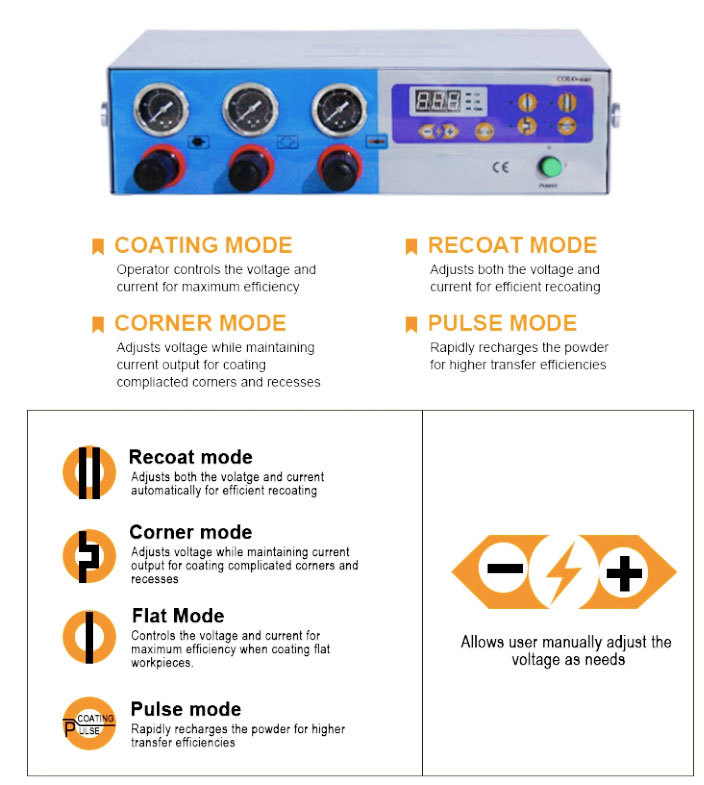
Intelligent Digital Controller
1:control powder charging: Adjustable 100KV voltage and current, Intelligent monitors for the working conditions;
2:Visual control panels: the voltage, current, conveying air pressure, supplementary air pressure, rinsing air pressure.
Benefits:
1: Faster Coating Speed, High Productivity;
2:Visual control panels: the voltage, current, conveying air pressure, supplementary air pressure, rinsing air pressure.
Benefits:
1: Faster Coating Speed, High Productivity;
2: Ideal for metallic and difficult powders;
3: Precise power output, powder saving;
4: Improved surface quality;
4: Improved surface quality;
5: increased powder penetration
6: Safety: Safe manual operation;
7: Maximum operation performance.
The difference between PaintGo660 and PaintGo 500 is that the 660 add a pulse mode and four pre-programmed options for processing:
Pulse mode could let the gun add more electric charge which will sharply promote the utilization rate of powder, save cost.
6: Safety: Safe manual operation;
7: Maximum operation performance.
The difference between PaintGo660 and PaintGo 500 is that the 660 add a pulse mode and four pre-programmed options for processing:
Pulse mode could let the gun add more electric charge which will sharply promote the utilization rate of powder, save cost.
4 pre-programmed options:
1: Re-coat Mode: Voltage and Current Pre-programmed suiting for recoating process;
2: Corner Mode: Voltage and Current Pre-programmed suiting for corner workpiece;
3: Flat Mode: Voltage and Current Pre-programmed suiting for flat workpiece;
4: Pulse Mode: Rapidly recharge the powder when change the powders;
1: Re-coat Mode: Voltage and Current Pre-programmed suiting for recoating process;
2: Corner Mode: Voltage and Current Pre-programmed suiting for corner workpiece;
3: Flat Mode: Voltage and Current Pre-programmed suiting for flat workpiece;
4: Pulse Mode: Rapidly recharge the powder when change the powders;

High Performance Cascade Gun
Patented high performance power coating gun provide excellent cascade powder spraying, and it's advanced high voltage electrode provide more ions on the powder, which could provide high utilization rate of powders.
Benefits:
1: Making more powder with ions, save powder materials.
1: Making more powder with ions, save powder materials.
2: Highest powder transfer efficiency, Higher efficiency;
3: Perfect powder distribution, Higher surface quality.
4: Quick-release coupling for the powder hose makes the powder change easier and quicker.
4: Quick-release coupling for the powder hose makes the powder change easier and quicker.
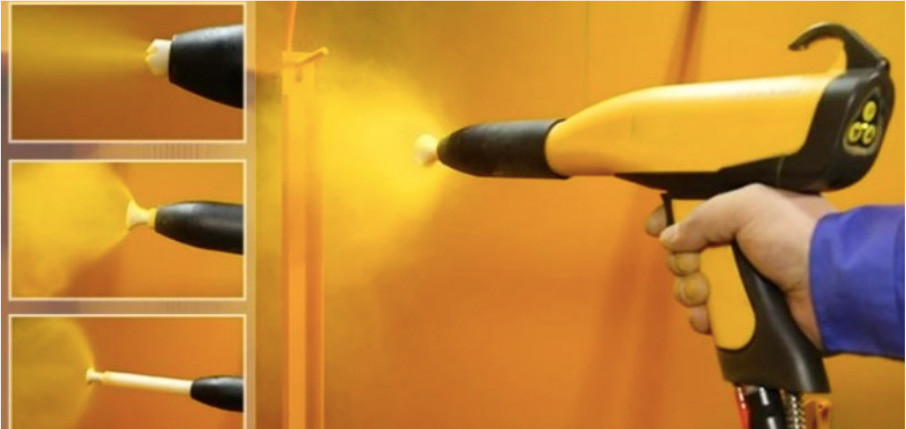
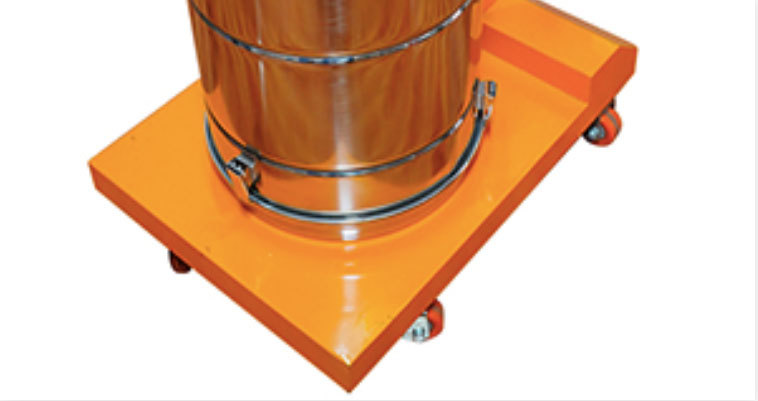
Powder Hopper+Trolley
Size: D36 x H52 cm; capacity: 50lbs powder
Powder hopper features durable stainless steel construction for ease of cleaning and minimized contamination.
The fluidizing hopper makes the powder completely fluidized without accumulation and absorbed moisture.
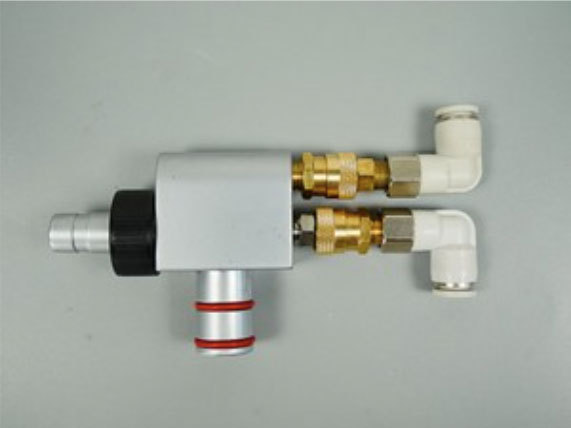
Powder Pump
Delivers more powders to spray guns using less compressed air, achieving efficient material utilization and lowered consumption costs.
A plug-in powder injector that can be detached without any tool, allowing fast cleaning and maintenance.
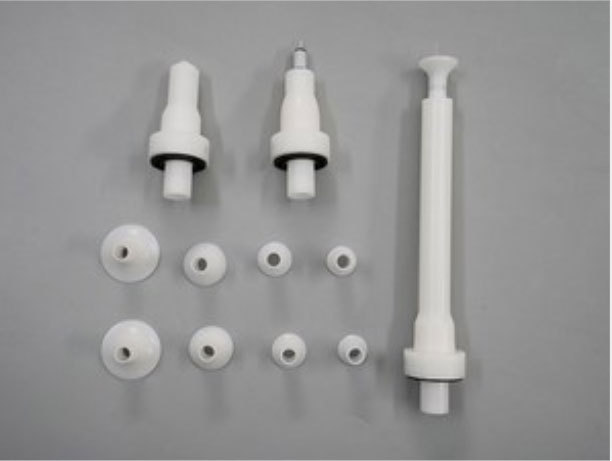
3 Types Spray Nozzle
ensuring a perfect powder atomization and charging.
non-stick material-great for color change.
1:control powder charging
2: Improved surface quality;
3: increased powder penetration;
ACMAN PaintGo-660 Could Avoid Orange Peel Effect and Back-Ionization
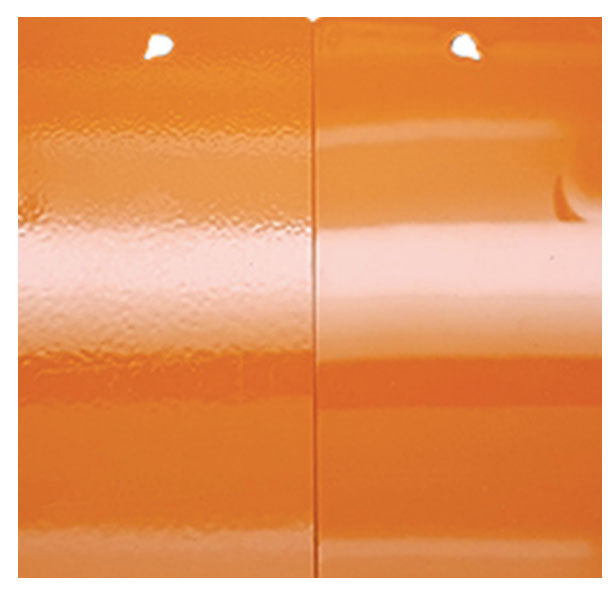
No orange peel effect
One of the most common quality issues with powder coating is an “orange peel” effect. Orange peeling is defined as an uneven texture on smooth finish products. It resembles the skin of citrus fruit, hence the orange peel name.
the Left one is the orange peel coating
Many things can cause orange peel defects. Here’s a list of common possible caused and what you can try to fix them:
the Left one is the orange peel coating
Many things can cause orange peel defects. Here’s a list of common possible caused and what you can try to fix them:
1: The heat up cycle of your parts is too slow. In this case, determine the heat up curve and increase accordingly. Parts with high wall thickness are especially susceptible.
2: Your substrate temperature exceeds the melt temperature, causing excessive film build. Try checking the substrate temperature (maximum should be 40ºC/104ºF). If it’s higher than the melt temperature, increase the cool down phase.
3: There has been a shift in particle size distribution and the portion of your reclaimed powder is too high. To fix, optimize deposit results of powder guns or increase lift intervals.
4:Your film thickness is too high or too low. Check system parameters to determine whether this is the case.
5: The powder coatings being used are incompatible. Check the booth and consult the powder manufacturer to ensure this is not the case.
6:The powder has been store too long or it has pre-reacted. To fix this, check the storage time. If powder is too old, exchange with fresher powder.
7: The voltage you're using is too high. To fix this, optimize the voltage or change to low ionizing applications or guns. guns charge particles by frictional contact with material inside the gun body, as opposed to the more widely used corona charging, which uses the power supply to charge particles. charging provides excellent faraday cage application.
8: You’re seeing uneven wall thickness. To correct, optimize the oven temperature.
You’re experiencing back ionization effect. Try reducing the voltage or increase the distance between the workpiece and the gun.
9: The airspeed at the oven entrance could be too high. In this case, reduce airspeed (it should be no more than 0.5m/sec or 1.5 ft/sec) or change air flow guides.
Parts are too hot when coming from the dry-off oven. Try allowing a longer cooler time (less than 40ºC/104ºF for parts.
10: The preheat temperature is too high. This can be corrected by lowering the preheat temperature or allowing more time for cooling.
11: The powder flow is too high. Too correct, lower the powder feed.
12: The coating time is too long. Too correct, lower the coating time.
13: The part geometry is difficult or unfavorable. In this case, try changing the hanging or gun configuration.
14: The gun and part are too close together. Try increasing the gun-to-part distance.
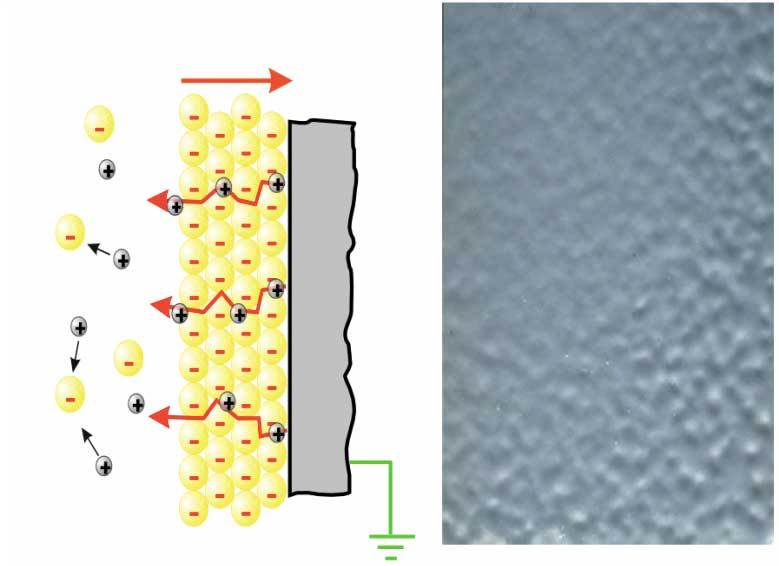
Back Ionization
Back Ionization is a problem in powder coating that occurs when the powder particles can’t find a ground point of the part’s surface and as a result build up unevenly on other particles on the part’s surface, this is often times referred to as “starring” or a “star burst effect”. The back ionization effect is more typical when applying a second coat on a part, but can happen when applying first coats as well.
Here are some tips on how to avoid back ionization:
Lower your voltage setting: This is the easiest step in avoiding back ionization; however you must always be careful when lowering the voltage (Kv), as it may cause further issues like unacceptable penetration and/or coverage. Powder Coating Equipment has factory pre-sets which automatically adjusts the voltage and current for this situation.
Coating from a proper distance: This seems to be the most common reason that back ionization occurs, when the gun is too close to the part that you are coating. Make sure to always coat from the proper distance, and then maintain that distance at all times. Many times this correlates directly with how the part or parts are hung on the hook/part rack. Make sure that the part is stable and not swinging, as this makes it near impossible to maintain the proper coating distance. In instances where the gun must be held closely to the part, it is necessary to adjust the current to compensate for this. Powder Coating Equipment has a factory setting for this as well.
Use an Ion Collector: A grounding ring or some other form of ion collector can be used as a ground source to reduce the rough surface effect. These are installed just behind the electrode tip and their purpose is to capture any unused ions from the charging process that can cause the uneven texture by overloading the surface with already deposited powder.
Technical Data
PaintGo-660 Powder Coating Machine | |||
Mains input voltage
|
220V
|
Operating frequency
|
50Hz/60Hz
|
Powder
|
50W
|
Output voltage(to the gun)
|
0-100KV(adjustable)
|
Maximum output current(to the gun)
|
180UA(max)
|
IP Index
|
IP54
|
Pneumatical data input pressure |
Min6bar(87PSl)/max.10 bar(145PSI)
|
Recommended input pressure
|
7 bar (1015PSI)
|
Max.Water vapor content of the compressed Air | 1.4g/m3 | Max.Oil vapor content of the compressed air | 0.1mg/m3 |
Max Air Consumption | 13.2 N m3/H | T Pulse | 15-20Clock/Sec |
Max Powder Injection | 600g/min | Polarity | Negative |
Options: Add Fluidizing
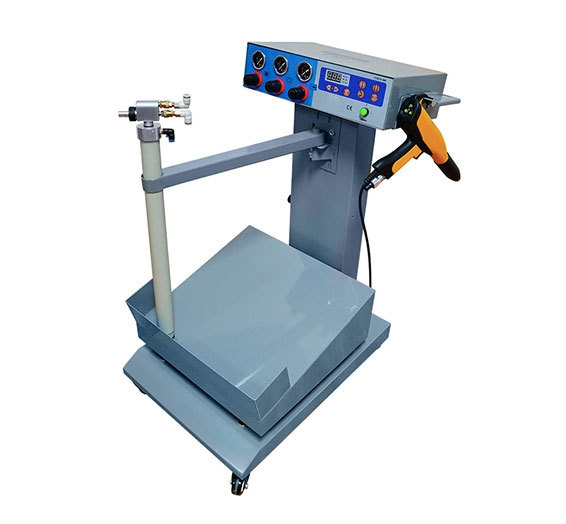
Vibration Motor for Fluidizing Powder
A vibrating motor in the trolley for fluidizing powder, ensuring there is no powder accumulation or absorbed moisture, feeds powder constantly and smoothly.
The vibration type do not need powder bin, the suction pipe could suck the powder directly from the original powder bags.
So, It is suitable for multi-colors changing processes, which could save changing time.
The disadvantage is that there is a little bit noise for the vibration.
The vibration type do not need powder bin, the suction pipe could suck the powder directly from the original powder bags.
So, It is suitable for multi-colors changing processes, which could save changing time.
The disadvantage is that there is a little bit noise for the vibration.
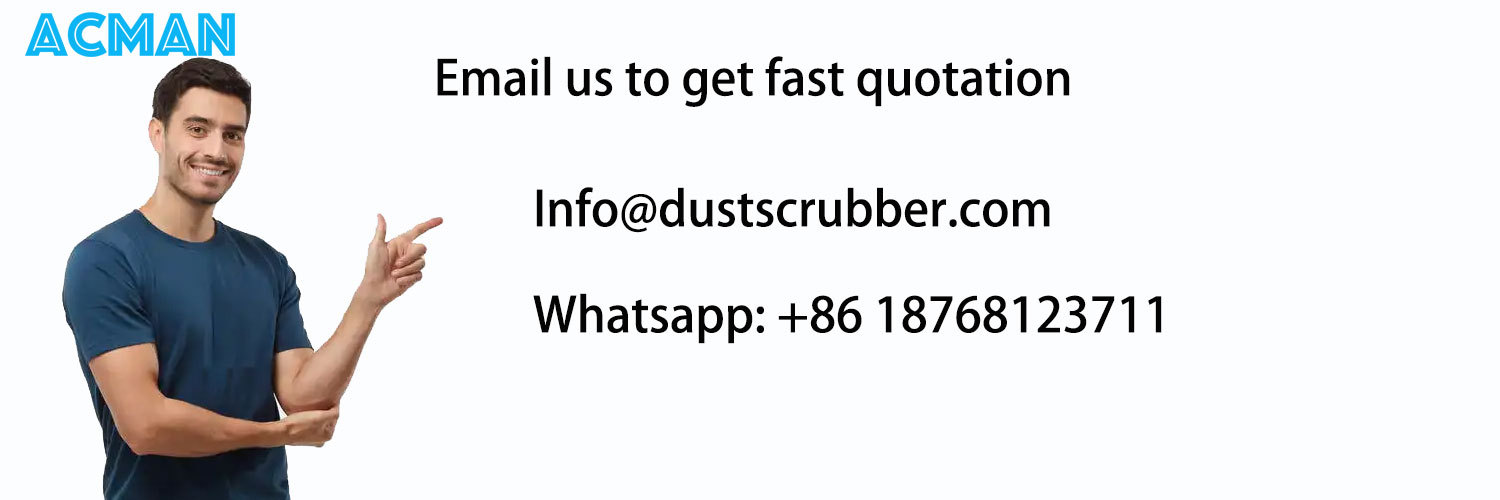
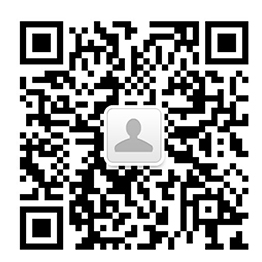
Wechat
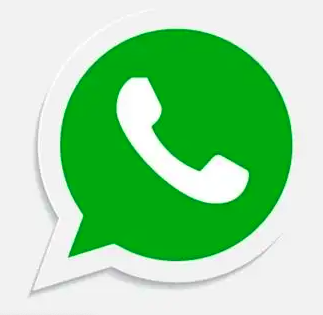
+86 19550289881
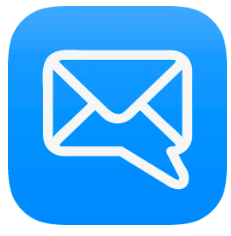
Info@dustscrubber.com

+86 18768123711
Related Products
Please send your message to us
- Tel
- *Title
- *Content
Love discounts? Subscribe to newsletter!
subscription
Send Inquiry
Please send your message to us
- Tel
- *Title
- *Content
Company
Categories
- Industrial Pulse Jet Dust Collector
- Cyclone Dust Collector
- Wet Scrubber
- Solder/Welding Fume Extractor
- Pharmaceutical Dust Collector
- Sandblasting Dust Collector
- Metalworking Dust Collection System
- Laser Fume Extractor
- PE Sinter-plated Filter and Equipment
- Dust Collection Auxiliary Equipment
- Central Vacuum Cleaning System/Unit
- Industrial Centrifugal Fan
- Sand Blasting Machine
- Bag In Bag Out Filter System
- Power Coating Machine/Powder Spraying System
Mobile Web
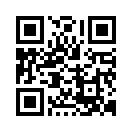